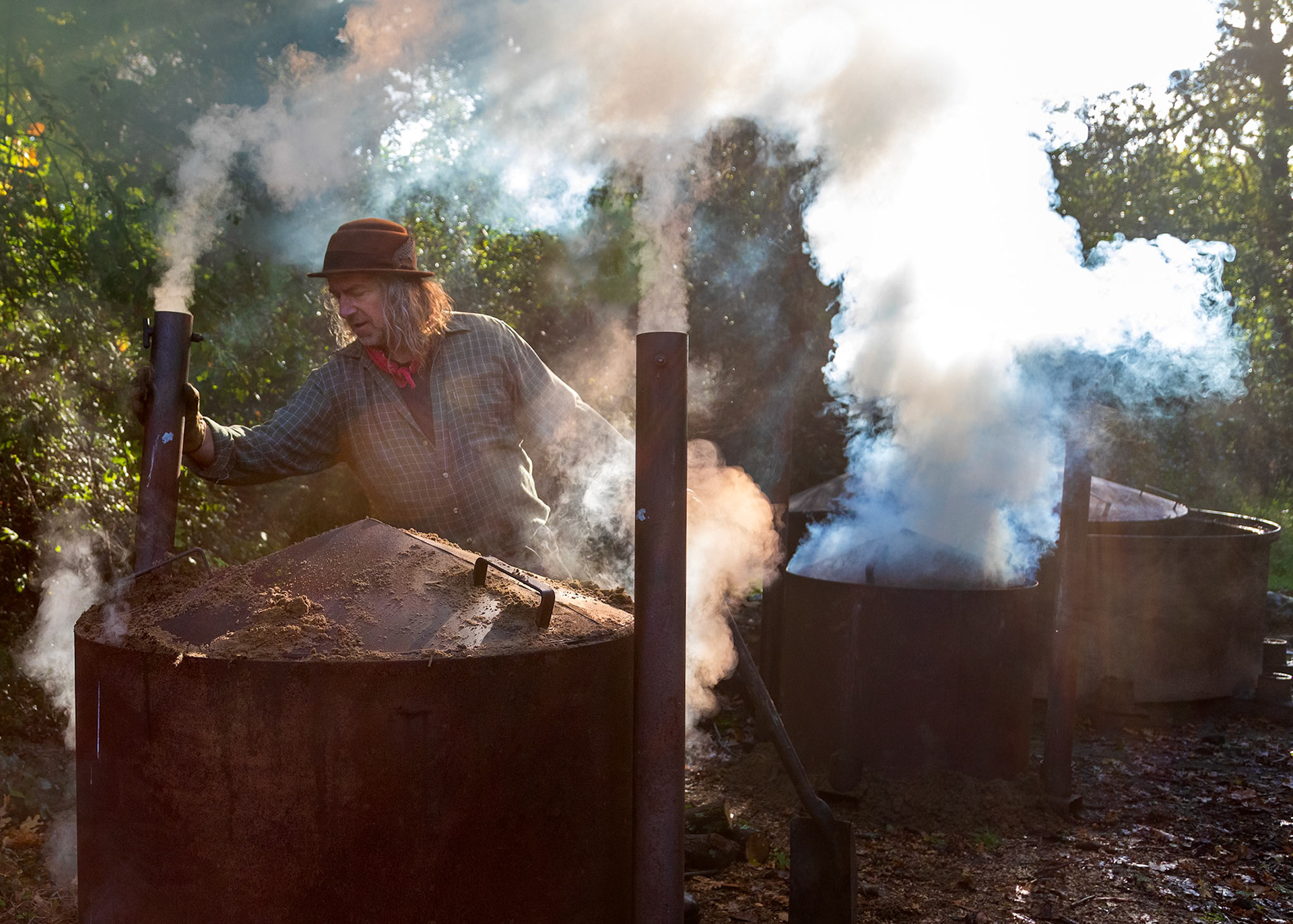
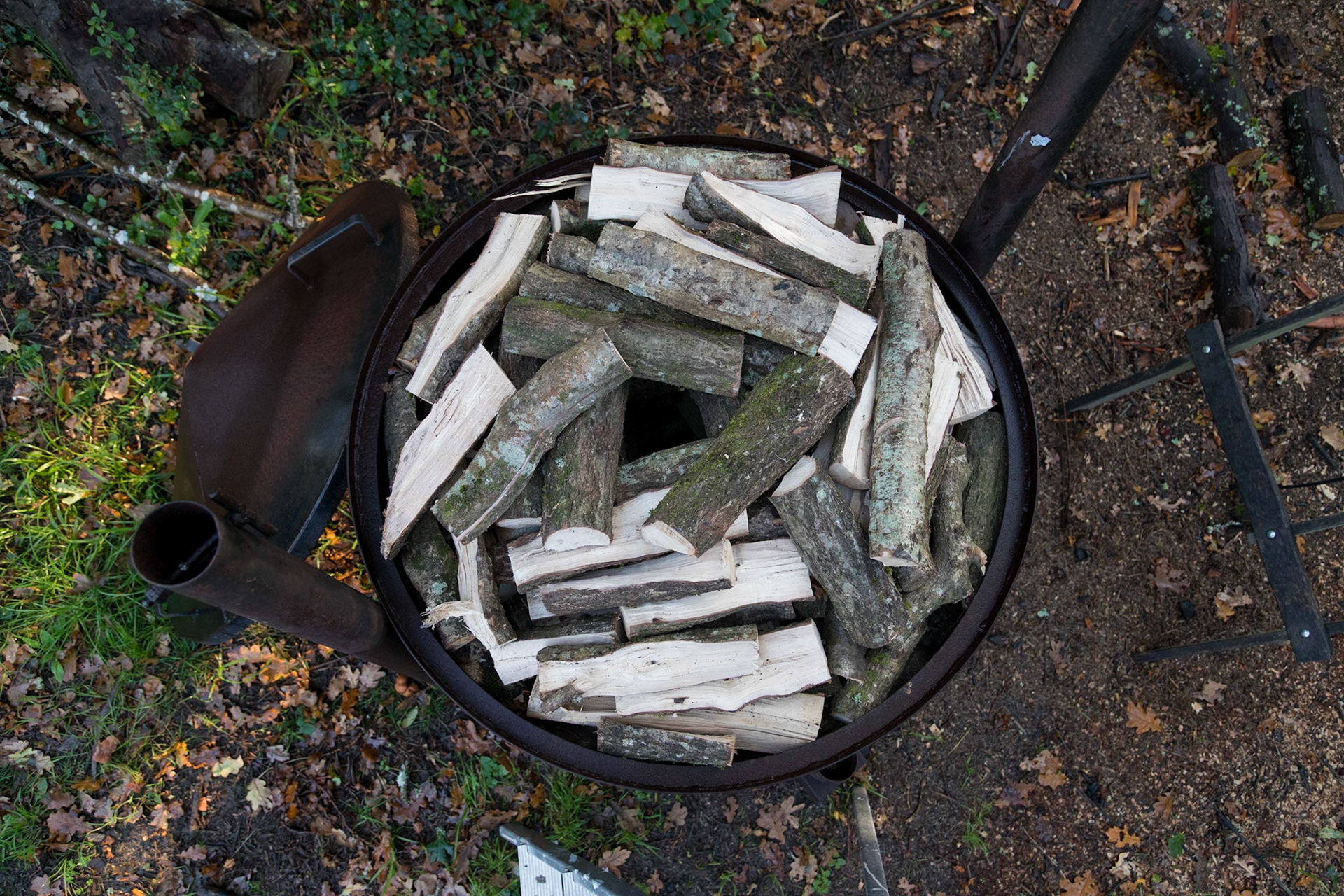
I met up with Graham early one winter morning in the woodland clearing. Over a cup of tea, he explained that his charcoal is made from locally coppiced woodlands in and around West Wight. He then talked me through the process of how to make charcoal from beginning to end.
Coppicing is an ancient way of managing woodlands, Graham tells me. It allows for the regeneration of shrubs, such as hazel. By regularly cutting the hazel at its base during winter months, the plant will send up new shoots in the spring.
The coppice rotation can be on a cycle of between 7 and 21 years depending on the plant species and the management requirements of the wood.
With the sunlight coming through onto the woodland floor, coppicing also enhances the fauna and flora by opening up new open areas for wildflowers and insects such as butterflies to flourish.
Coppicing is a form of woodland management that can traced back hundreds of years and was traditionally used as a way of producing household and agricultural products as well as firewood and of course charcoal.
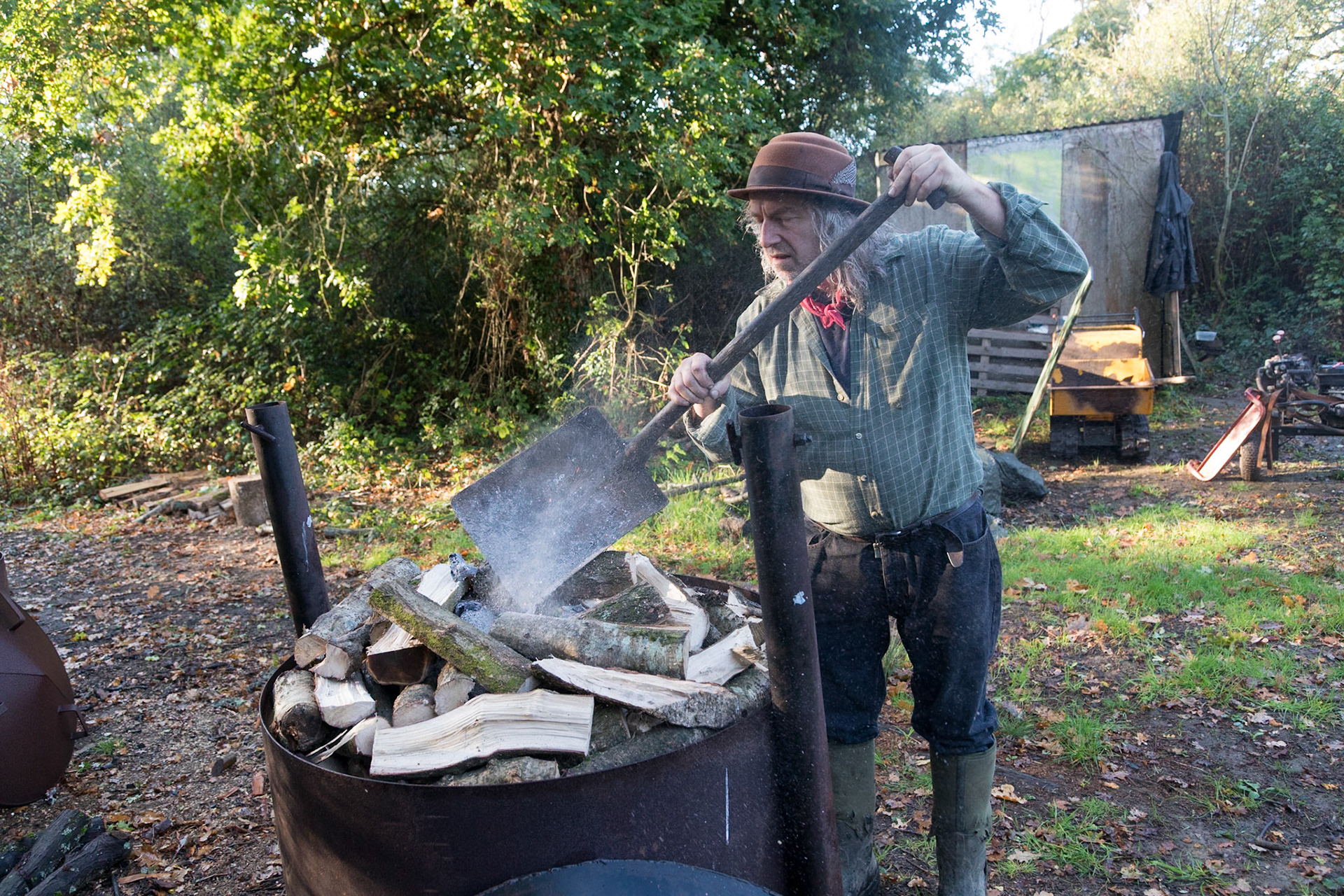
Adding embers to the kilns.

Graham Hardy adding embers to the kiln
The kiln is loaded to the top leaving a central chimney which allows the embers to be poured down the centre to the old charcoal to light the fire. Once the fire is alight it is left to burn, this is called the freeburn, which lasts approximately one to two hours.
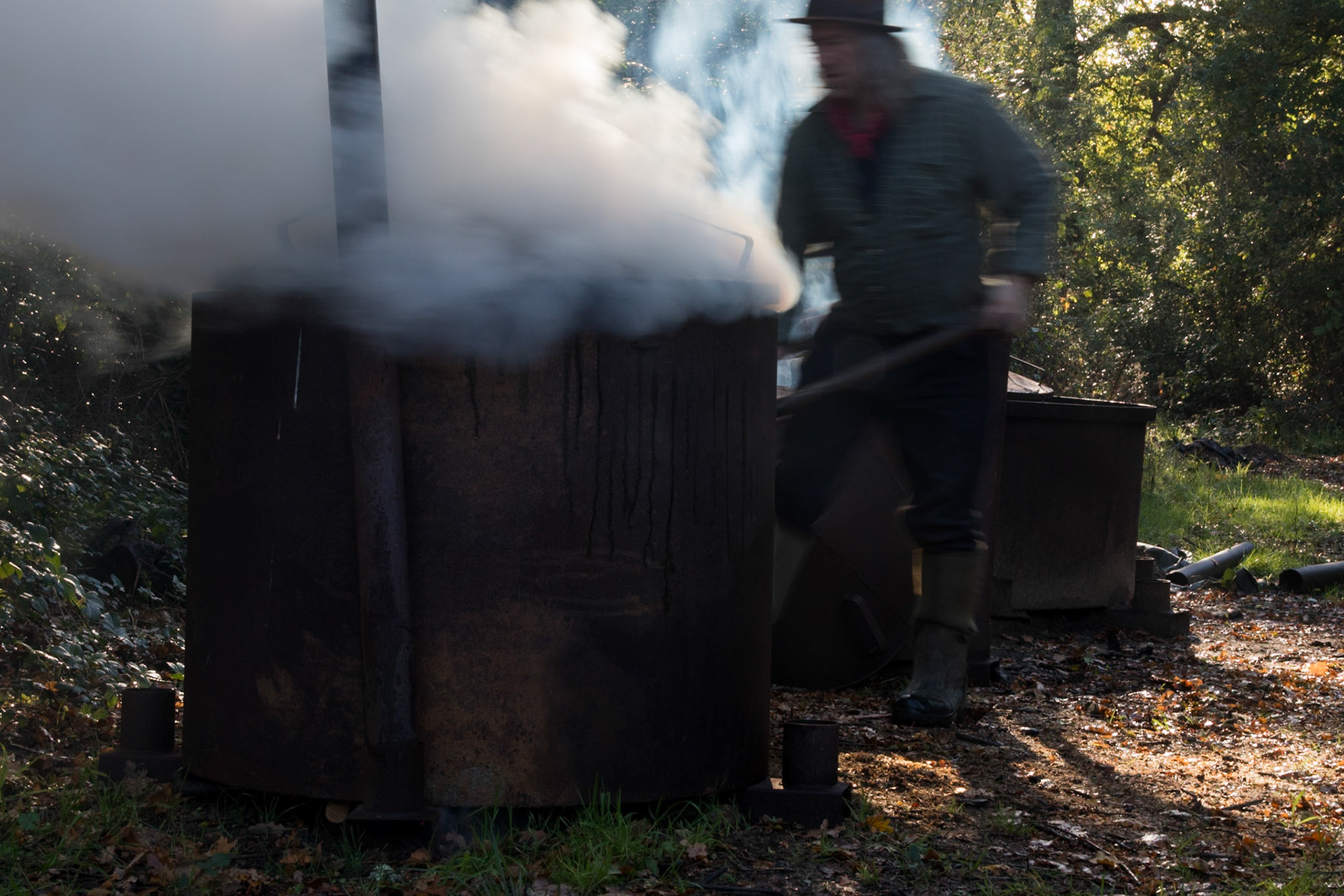
Over time the smoke will change colour from white to a dirty white and the smoke volume will decrease. It is important to monitor this stage closely because if the smoke reduces and turns blue then the charcoal is being burnt and only ash will result. The next stage is to close the airflow and to seal the two chimney ports. Timing is critical here and is done just prior to the smoke turning blue. Once the kiln is closed it will continue to burn for at least another two hours until all the air is burnt off and the fire is extinguished.
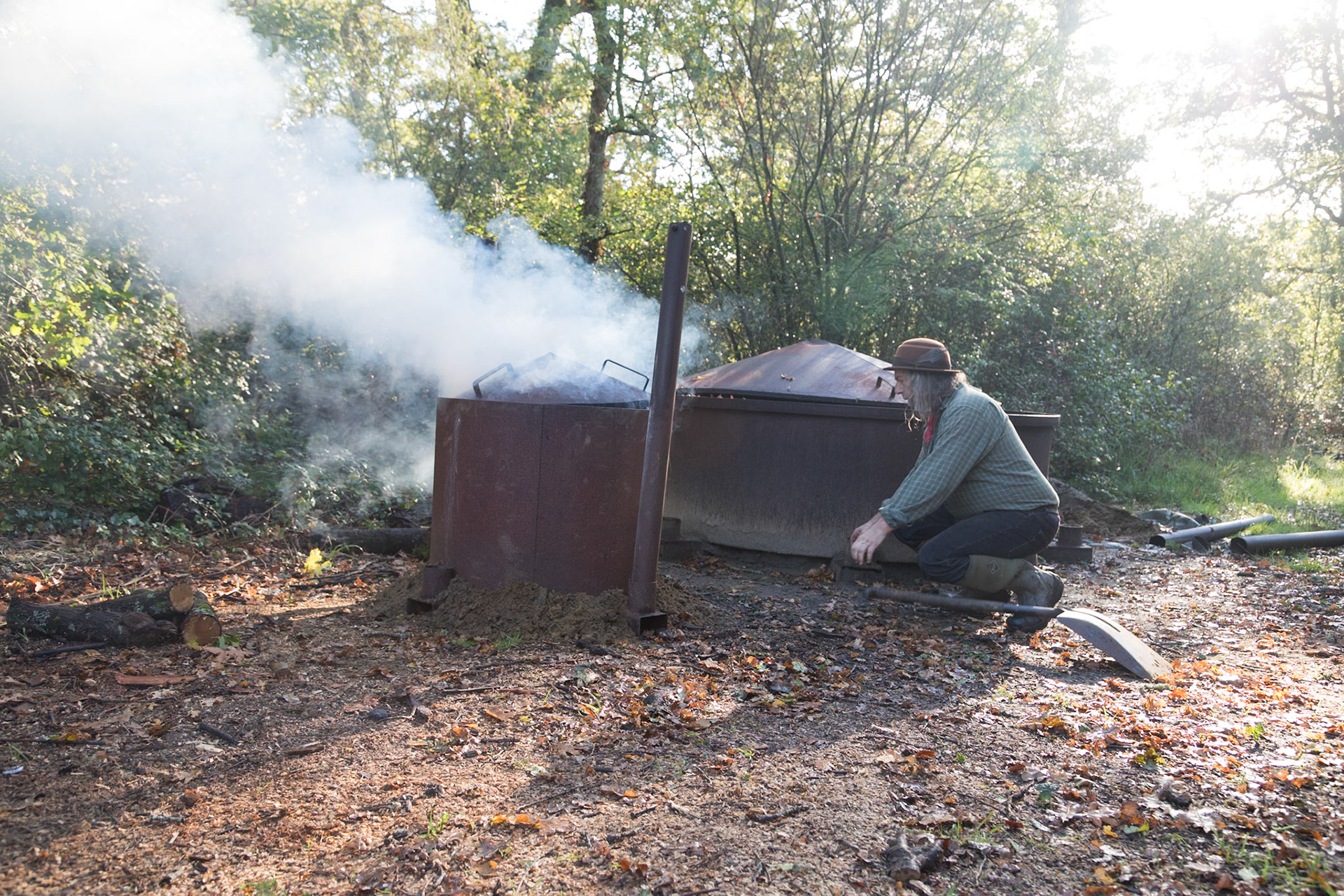
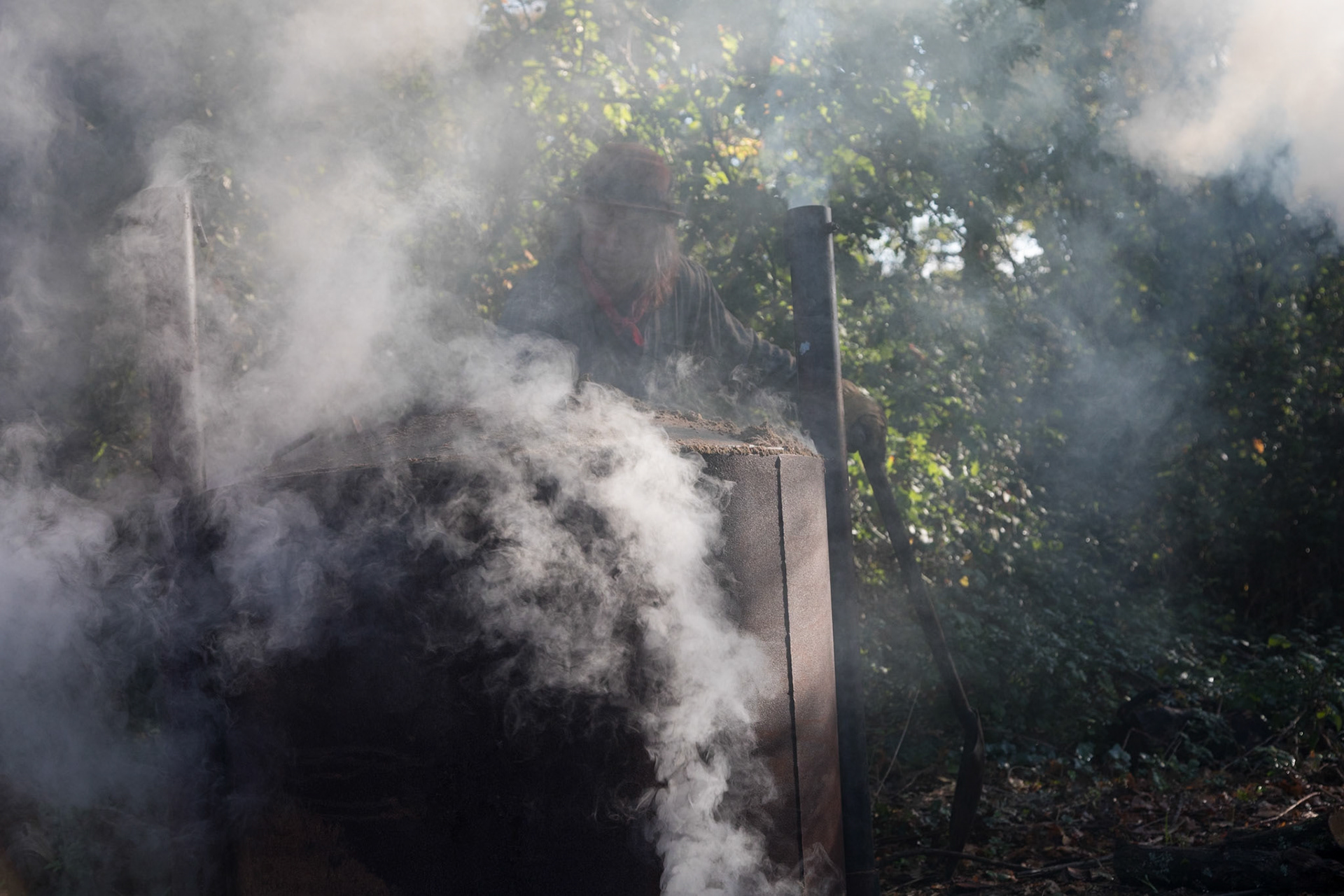

Graham is keen to encourage the use of locally produced charcoal on the Isle of Wight rather than it being shipped in from abroad from unknown sources, where the sustainability value can be pretty low or even non-existent. At least with Island produced charcoal, Graham explains, you can be pretty sure that the charcoal is of high quality, the product miles are low and you get excellent results when cooking.
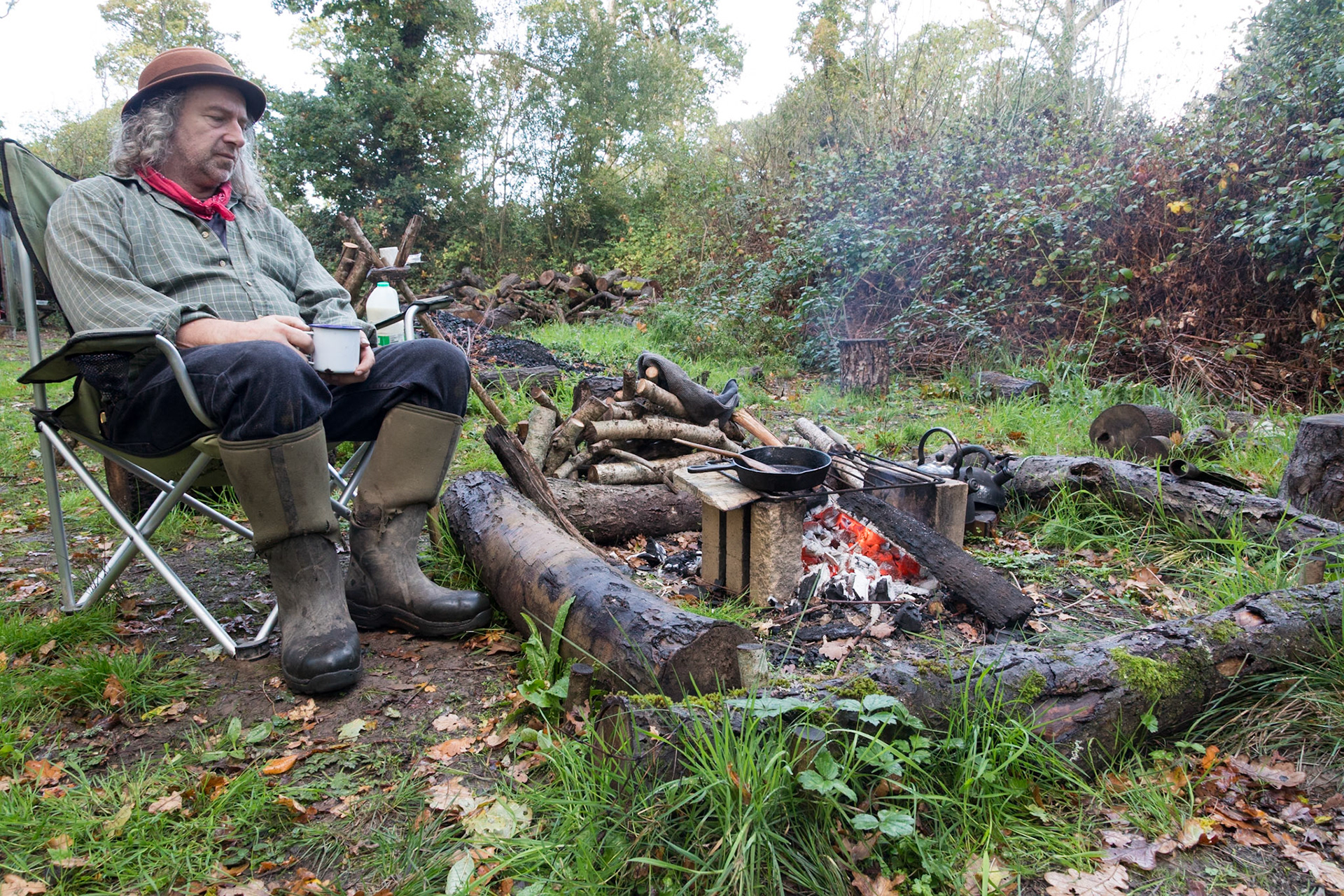
Graham enjoying a cup of tea around the camp fire. After years of making locally souced charcoal, Graham decided to retire in 2024. The search is now on to find someone else to carry on this woodland craft business.